汽车线束企业柔性生产线优化研究
嵇岗 上海李尔实业交通汽车部件有限公司 摘要:汽车电子电气系统中重要的线束系统在大规模批量式的生产模式下已经不能满足现代社会的发展需求和客户日益提高的要求,需要对其进行优化。本文POLO KSK主线束的柔性生产线进行优化,详细介绍了如何在JIT/JIS环境下设计和安排生产线已满足客户小批量多品种的要求通过实施优化,公司在准时发运率的指标上提升了许多。 关键词:汽车生产,柔性生产线,线束生产企业,资源配置 1、引言 制造企业正面临着准时交货、提高生产效率,提升产品质量、降低产品成本以及对市场需求做出及时响应的多重压力,这些严峻的形势迫使人们认识到提升生产制造系统的柔性对企业获取竞争优势,保持稳定的盈利性可持续发展目标具有极为重要的战略和现实意义。“柔性”通常理解为是对环境不确定性的一种适应性的响应,而提高企业的生产柔性简单地说就是指增加企业在生产制造过程中灵活性和快速应变能力,优化资源配置,提高生产流程的弹性,以较低的资源成本来满足客户的快速需求。作为汽车电子电气系统中重要的线束系统,常见的大规模批量式的生产模式已经不能满足现代社会的发展需求和客户日益提高的要求,一切以客户的价值为出发点,创造连续流动的价值流的柔性生产模式和管理方法成为先进生产模式的代表。 2、生产流程优化及柔性生产线在线束生产企业中的实证分析 我们所接触到的传统的流水线通常是U形流水线,这样的流水线布局也是一般被认为是比较经济和精益的方式之一。它比较适合于大批量生产,能大幅提高生产效率,降低成本。但对于小批量多品种,并且需要按照JIT/JIS的供货模式来说,传统的生产线将无法满足客户和市场的需要。这就需要采用更为柔性的生产线来加以应对。 柔性生产线的方式有很多,主要是在精益生产的思想下,对生产线进行必要的自动化调整以提高生产柔性和生产效率,消除生产瓶颈。在当今的汽车工业中以KSK模块化的JIT/JIS供货方式已经成为先进汽车制造企业的主流趋势。为了应对需求随时变化的模块化供货,汽车线束企业必须采用多条生产线结合的方式来加以应对。这里我们将以上海大众POLO的KSK主线束来探讨这种生产线是如何优化生产的。 对于成品的总装线生产,需要区分基本模块和选装模块。基本模块是最大的模块,它包含了所有基本的配置功能,所有的车型配置都必须采用。而选装模块(或称选装包)则是根据不同的车型配置而不同的,终端客户可以根据自己的喜好而进行选择,这也就是客户需求发生变化的最根本的来源。以上海大众的POLO生产线为例,整车厂发给线束生产企业最近的窗口时间仅为2小时,这就意味着,当线束生产企业收到客户EDI明确的线束序列号之后必须在2个小时内完成线束的生产,包装,配送等过程,而且必须是按照系统传递的次序按时送到客户的总装车间特定的工位上。其生产的操作难度比较大。因此,对于此类线束的生产我们需要对生产线进行必要的调整。常规的线束生产线是一条U形的旋转生产线,每条线束从第一个工位开始生产到最后一个工位结束就完成了一条线束的生产过程而后进入测试和包装程序。这种方式适用于批量规模化的线束生产,但无法满足JIT/JIS的要求。而对于POLO的主线束生产线必须由基本模块生产线和配套的选装模块生产线共同协同完成。这种柔性化汽车线束生产线主要表现形式是以基本模块的自动化生产线为中心,不同的选装模块生产线环绕的方式来进行生产(见图1)。 ![]() 图1Polo KSK主线束柔性生产线布局图 由于POLO主线束是汽车线束总成中最大的线束,通常有5-8米长,因而其基本模块的生产已经不能在常规的线束生产线上进行生产,需要采用H形总装配板来组合基本模块线束的生产线。其生产线由14块H形装配板组成。由于PGTF生产线本身是自动化的柔性生产线,其可以根据线束的复杂程度和工艺来灵活的调整装配工位的数量,并且可以调整生产线运行的速度。该基本模块生产线位于整个生产区域的中心位置。 选装模块生产线则位于基本模块生产线的周围,由于选装模块的线束一般都较为简单,且并非每根线束都需要安装,只是根据最终客户的选装要求才进行生产,因此,通常这类线束的生产只安排单工位生产单元的模式,由1-2名员工进行生产(图2)。 ![]() 图2POLO KSK主线束选装模块生产单元 那么,大众POLO KSK主线束的柔性生产线是如何运作才得以保证客户快速的要货需求的呢?这里我们将简要阐述其运作过程。 我们已经知道上海大众发布给供应商的最后一个时间窗口是两小时,也就是说客户提前两个小时通过系统将EDI信息包(R100)传输至汽车线束生产的现场(图3)。EDI信息包中包含了整车厂总装生产线上的所要生产的车型的车架号(K号)以及该车的所有配置(基本模块和选装模块的组合),同时也显示了该车通过整车厂总装线线束安装工位的时间。该EDI指令要求线束生产商在指定的时间按照指定的车架号和配置表生产线束总成,并及时送达总装线工位。 ![]() 图3汽车线束模块供应链 线束生产商在收到客户的EDI信息包后,首先需要按照系统所提供的每个车架K号所要求的线束信息打印出来,线束主要信息以而维条形码的形式出现。线束总装现场的员工用扫描装置进行扫描后,生产线计算机系统将自动识别并分析该信息,并迅速形成以唯一K号为标准的作业配置清单,里面涵盖了所有需要的选装模块。该作业清单是客户拉动需求的看板卡的一种表现形式,是线束装配生产线生产的唯一指令凭证。该生产指令分别下达至基本模块总装线和选装模块生产单元。选装模块生产单元之间由模块线束运输车相连,每台运输车上所有的选装模块线束代表唯一的一根主线束的所有附件将被运至总装线工位(见图4,图5)。由于每个选装模块生产单元有5件缓冲,所有当订单指令下达时,能迅速按照排序系统中的线束选项立即从选装模块生产单元中通过运输车将所有的选装件收集并与基本模块同时生产。同时,为了防止选装模块的配置发生错误,在运输车完成所有的选装模块运输任务后,需要有专门的人员再次对所有选装模块线束的条形码进行分别扫描,系统将分析和核对该运输车上所有的选装模块线束是否与客户的车架K号所要求的配置是否一致。只有在所有的核对信息均通过无误后,才允许该运输车进入基本模块总装线。 ![]() 在主线束最后完全装配后,操作人员将其放入测试区域,将K号进行扫描后,测试系统将自动识别并选择相应的测试程序,对其进行严格的自动化测试,如导电性能,放水性能,装配完整性测试等。只有在完成所有测试合格之后,测试系统才能授权打印出合格的标签。标签上有线束的型号,对应的车架号,生产时间,生产位置,公司名称等,以便于后续线束的安装和追溯。最后线束将按排序系统进行包装和发运,按时将线束送达至整车厂总装车间生产线的制定位置。 通过以上基本模块生产线与选装模块生产线的协同生产,从而我们能够保证在多品种小批量的情况下,保质保量的按时以JIT/JIS的形式向整车生产厂持续供货。 3.实施效果评估 本人所工作的线束生产企业在实施了生产计划的柔性管理之后,在准时发运率的指标上提升了许多。2014年的平均发运准时率为82.83%,而2015年在进一步提升柔性计划的基础上,实现了年平均发货准时率96.67%,这在目前汽车整车企业要求供应商实施JIT/JIS的大背景下是非常难能可贵的。为此开发了基于WEB平台的企业绩效指标系统,每月输入并跟踪分析所有的指标,系统自动形成相应的数据表格,并结合整个部门乃至公司的绩效综合考评。 结束语 本文仅研究了线束工厂的内部生产环节的柔性,几乎所有的国内外文献资料也仅对内部的生产柔性进行分析和研究。而理想的柔性管理需要将整个供应链的上下游供应商和客户都联系起来,实现联动柔性,这样才能优化整个供应链上的价值链,并实现真正理想化的柔性管理。对于这方面的研究还有待我继续学习和总结。 参考文献 [1]李杰.战略柔性理论与实证述评及启示.理论与改革,2008,6:93-94. [2]黎民炼.浅述模块化供货方式.机电工程技术,2002,31(6):17-18. [3]张林艳.汽车零部件制造工艺与柔性生产线.市场纵横,2004,7:36-37. |

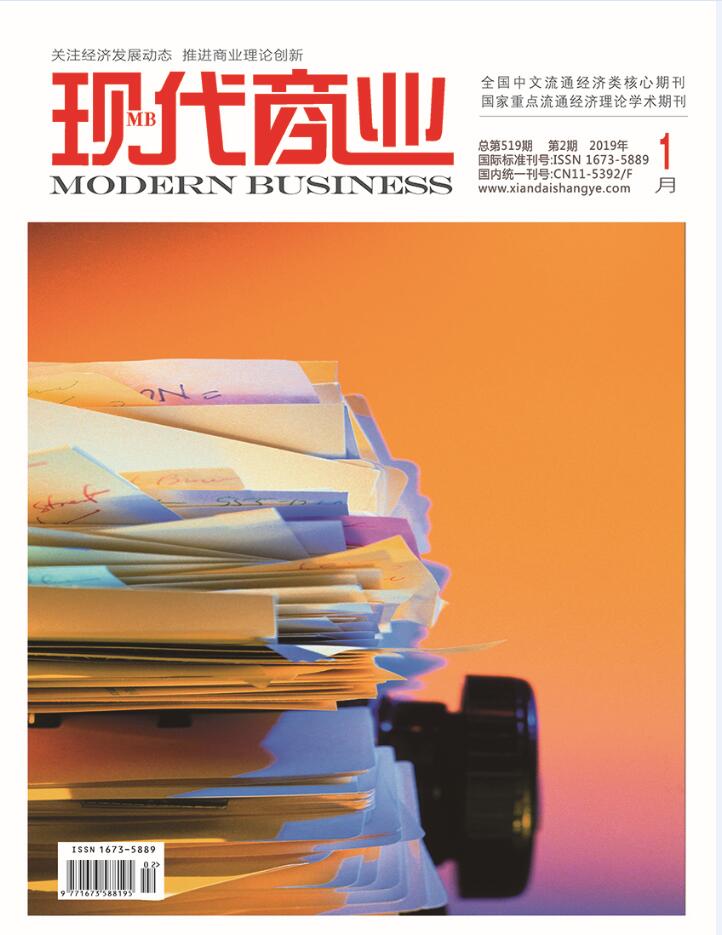
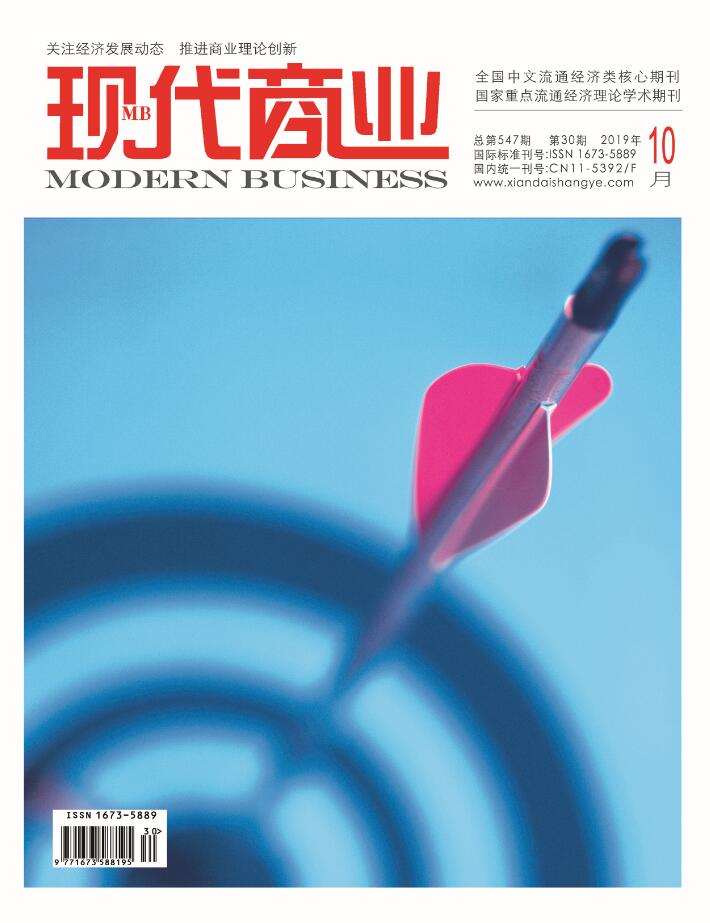