精益生产在汽车零部件企业生产管理中的应用
周家华 华南理工大学 摘要:精益生产作为世界知名的先进管理理念,在国内外得到了广泛应用与认可。本文以X公司的精益生产应用为研究对象,通过现场实地调研以及专家访谈等方法,指出了X公司生产管理存在的问题,利用应用生产线平衡、快速换模等精益生产工具,结合ECRS、5W1H等IE分析方法对这些问题进行优化,减少了企业的浪费,降低了制造成本,提高了生产效率。对优化后的效果分别进行评价,并通过建立管理体系,确保改善方案的顺利实施。X公司希望通过实行精益生产,帮助企业消除浪费,降低成本,不断完善自己,提高企业的竞争能力。 关键词:精益生产;生产线平衡率;全面生产维护;快速换模 一、引言 近十年,我国的制造业发展迅猛,但与世界其它先进国相比,我国制造业的基础依然较弱,明显存在着发展的不可持续以及不均衡等问题。在产品质量、技术水平、企业内部管理水平、自主创新能力等方面尚未达到新型工业化的要求。 制造业是我国国民经济的一个重要组成部门,而汽车工业又在制造业中占据非常重要的位置。中国加入WTO后,发达国家的各大车企通过合资或技术战略合作等多种形式积极进军中国汽车市场,为中国汽车行业的快速发展提供了巨大机会与诸多挑战,进而促使中国汽车市场的蓬勃发展。 近几年中国汽车市场增速明显下滑,面对这种市场态势,各大汽车公司纷纷采取降价促销等策略吸引客户,面对需求的减少,各大车企不惜通过减产等方式来缓解日益增长的压力。2010年到2019年全国汽车产销趋势目前,全球汽车工业正值寒冬。地缘政治所引发的经济不确定性和地区冲突,对汽车行业产生了很大的影响。随着管理成本以及人工成本的不断上升,面对销量的下滑,以及未来的不确定,包含汽车零部件配套企业在内的整个汽车制造业都更加需要从精益理念出发。 精益生产起源于1932年的日本丰田公司,是一种先进的企业生产管理方法,以有效地消除各种资源浪费为原则。几十年来,在国内外许多行业中得到了广泛的应用,并取得显著的成效。随着输入开展改革开放,越来越多的国内企业意识到了现代管理思想在企业发展过程中起着重要的作用。汽车行业一直属于精益生产应用的佼佼者,以长春一汽为代表的著名企业首先引入了丰田生产模式,并取得了较大成果,这引起了一股研究和推行精益生产的热潮,进而从过去落后的生产管理模式转向了系统化现代管理模式。 二、精益生产的概念及原则 (一)精益生产的概念 精益生产是起源于丰田生产方式的一种管理方法,它包含了国际汽车发展计划的多位专家教授对丰田生产方式的不断探索与研究[1]。精益生产通过把精益思想注入到企业的组织架构、生产流程、开发设计、质量管理等各个方法,使企业的生产流程联系得更加密切,能够及时、准确地满足客户个性化和多样化的需求,消除工作环节中不增值的各种浪费,提升产品质量,从而达到提高企业竞争力的目的。 精益生产的改善活动主要是围绕着“精”和“益”两个方面所进行[2]。所谓“精”意为精简、精细、精准,其目的在于通过识别生产及流通环节中的价值流,减少或消除非增值的活动,从而简化流程、降低成本,减少不必要的损失[3]。所谓的“益”是对精益求精的追求,意味着精益生产是一个持续改进的过程。 当前,精益生产普遍被定义为:以客户需求为导向,通过“5S”和全面生产维护(TPM)等改善生产现场,利用看板管理及准时制生产方式减少库存,通过六西格玛、全面质量管理(TQM)等提高产品的质量,坚持“产品质量是生产出来的,而不是在后期检验出来的”理念,不断降低成本,进行持续改善,从而实现利润的最大化[4]。 (二)精益生产的原则 不断发现企业存在的浪费,并积极地采取相关改善对策减少或消除这些浪费,通过持续改进不断完善,从而实现价值的最大化是精益生产管理的核心理念[5]。在减少和消除浪费的过程中,会发现产品整个生产过程中存在的问题,这就需要优化整个生产过程。从高层领导到普通员工,企业的所有部门都要深入了解精益生产的核心理念和基本原则。下面是精益生产的五大原则: 1.价值原则。精益生产活动的价值始于对客户需求的定义。企业应该始终从客户的角度来看待企业的产品或服务是否具有价值,可否能为客户带来等值的回报[6]。任何无法为客户创造增值的环节或服务都被视为浪费,企业需要竭尽全力去减少或消除这些不必要的浪费或者非增值的活动。 2.价值流原则。价值流是指完成客户的需求所需要的步骤或活动。它包括增值和非增值部分,并且显示物料及信息的流动情况。精益生产所谓的浪费,就是指消耗资源但无法增加价值的活动,属于价值流里的非增值活动。识别价值流实际上也是一个识别浪费的过程。 3.流动原则。不管是大量生产方式还是精益生产,流动都至关重要。企业在流动过程中能够非常明确地认识到浪费的存在,才能及时地采取措施消除浪费,从而实现价值最大化。 4.拉动原则。需求拉动是根据客户的需求进行生产,由客户控制资源的流动,使客户在需要的时候得到需求数量的产品,这避免产生库存堆积、生产等待以及其它多余的浪费,从而最大限度地降低成本,实现产品价值的最大化[7]。 5.尽善尽美原则。所谓尽善尽美既精益求精,企业在经历前面四个关键环节之后,将在各个方面都会有较大的进步,而持续改善是永无止境的,需要不断地改进企业存在的不足之处。 三、现场问题诊断—以X公司为例 X公司成立之初恰逢中国汽车市场的蓬勃发展,企业在高速发展期重点基本放在了达成产量任务,所以在管理上并不够精细。近些年随着产量的低迷,一些生产管理上存在的问题逐渐显现出来。通过对X公司生产现场的实地考察以及与运营部门的相关专家们的面对面访谈,对公司的生产经营状况以及公司存在的问题有了一定的了解,经过对收集到的数据进行分析,发现X公司在未深入实行精益生产前存在着许多问题。 (一)生产现场存在的问题分析 1.生产线平衡问题 座椅组装车间有四条座椅装配线,其中#2前座椅装配线是X公司目前主要的生产线,该生产线包含30个工位,装配员工共计32名,工作内容为组装、测试和检查。X公司的座椅装配线的工序较多,该流水线基本为人工操作,存在员工之间的劳动负荷不合理,工序间的操作时间不平衡的问题。其中有些工序操作时间只需几十秒,但有的工序需要百秒以上才能完成工作,阻碍了生产效率的提高。 2.自动化率低 X公司的座椅与发泡生产过程中大部分工作都是由人工完成,尤其座椅组装线几乎所有工序都是人工操作,自动化率非常低,这不仅造成了人工及成本的浪费,影响产品质量的稳定性,也降低了生产效率。 3.换模效率低 因客户生产计划频繁变化,以及售后件等加急订单的插入X公司发泡车间平均每天要进行6次左右的换模,每次换模需要435秒左右的时间,每天发泡线因为换模造成的停线时间大约40多分钟,严重影响了X公司的生产进度和生产效率,这给X公司造成了较大的浪费。模具区域的规划,员工熟练程度、事前准备、标准化的作业和事后工作的完善都会对换模效率产生影响。X公司换模流程存在不合理的地方,导致一些可以提前准备的工作需要在换模过程中做,增加了换模时间。除此之外,换模工作的分配不合理,有些可以同步进行的工作,没有并行去做,造成了操作时间的增加。 (二)问题成因分析 一个企业要做好精益生产管理理念的导入与执行,管理层的意愿至关重要,只有在管理层向公司上下展示管理层对精益生产的重视程度,才能够从根本上带领公司全体员工一起参与到精益生产的应用管理当中。X公司虽然也曾导入过精益生产,但在执行过程中还是存在很多不足,主要有以下几个方面的原因: 1.精益生产理念的普及不足 精益生产活动是需要让全体员工理解、支持并参与的活动。从X公司目前的状况来看,精益生产的理念大部分都停留在管理层的交流传递,基层的一线生产线员工对精益生产的了解很少。举个例子,很多一线员工认为只要一天完成了当日生产计划的数量,不管每小时生产速度是否均衡,是否因为生产速度的不均衡影响了生产运营部门的工作,只要完成工作任务就可以。虽然生产线的很多指标是和精益生产有关的,但是一线员工并没有真正理解指标的涵义,只是被动地接受从上面传递下来的命令。 2.激励制度不健全 除此之外,X公司的激励制度和奖惩制度不够健全,对提出好的持续改进建议的员工应该进行一定程度的奖励,从而使发员工们积极提出改善方法或积极参与改进活动中,激发员工的积极性。 3.沟通渠道不畅通 企业的沟通通道是员工向上反映问题和领导向下传达指令的有力工具之一。如果交流渠道不畅,这就造成了企业无法有效执行上传下达,不仅员工在日常工作中发现的一些好的改进想法和建议无法有效传递,领导向下传达的命令也很难被快速且有效地执行。 四、基于精益生产的生产现场改进方案 (一)生产线平衡优化 #2座椅装配线是目前X公司的主力生产线,此生产线属于多品种混线生产的U型生产线。在生产过程中,每个工位的生产所需时间无法保持一致,存在工位间生产节拍时间的不同,这会导致生产节拍快的工位的等待浪费,造成工时的浪费。X公司需要通过工位的取消、合并和重排等方法,以及自动化设备的应用,提高了生产线平衡率,减少了生产过程中的浪费现象,从而降低了制造成本。 生产线的瓶颈工位指的是一条生产线中耗时最长的一道工序,它限制了整条生产线的生产效率,这需要我们通过不断改善瓶颈工位,提高整条线的线平衡率。本文在各工序数据的收集过程中,主要采用了现场测量和访谈的方式。首先仔细观察和记录需要统计的工位作业顺序,将每个工位作业的步骤一一分解并记录下来,然后使用秒表进行计时。需要对每个工位的操作进行五轮的记录,记录轮数越多,数据会越准确。记录完毕后,把每一步骤的横向操作时间求平均值,所得出的数值就是这一步骤的净操作时间,之后再把静操作时间列进行求和,得出的数值就是该工位操作所需时间。数据收集的示例图如下表1所示: 表1 工位数据收集示例表 ![]() X公司#2装配线的每月客户需求量为15,840台,设每个月有22个工作日,公司实行双班制生产,由此得出平均每天的生产量为15,840/22=720台。去掉午饭及晚饭时间以及其他休息的时间,生产线员工每天每个班次工作9小时,因而计算出该生产线的节拍应为:TT=2x9×60×60/720=90(s),90秒为此生产线的生产节拍。 根据上述各工位数据资料,对#2装配线的线平衡情况进行了分析,得出下图1所示的生产线平衡图: ![]() 图1 #2座椅装配线线平衡图 从#2座椅装配线平衡图中可以看出中,FS01-2工位滑轨安放+蒙皮泡沫安放+包滑轨的实际操作时间为110秒,高于需要的生产节拍时间90秒,是此生产线的瓶颈工位。 计算得出当前该生产线的线平衡率P=2060.2/110*30=62.43%,从这一数字中我们可以看到,#2座椅装配线的线平衡率比较低,远远不及公司设定的生产线平衡目标80%,存在严重浪费现象,应实施装配线平衡优化。 所谓生产线平衡优化就是使用精益生产和工业工程方法对生产线进行改善,达到生产线平衡的效果,使其更接近生产节拍。本文ECRS与5W1H等方法对#2座椅装配线的各个工位进行改善分析,通过对工位作业内容的重新划分与调整,提高生产线平衡性。 1.#2座椅装配线有30个工位,其中两个工位的作业时间超出了生产节拍时间,因此需要首先重点改善这两个工位。通过运用ECRS和5W1H分析法提问,确认问题的原因,制定解决方案。 经过上述提问的方法,将FS01-2中固定蒙皮到滑轨的工作和FS01-4的半成品拿取搬运工作合并成为一个工位,并取消了FS01-3的坐垫整理工位,既减少了人员,又减少了FS-02的操作时间,经过工位的取消与部分工作的重新合并,FS01-2的操作时间变为70秒,减少了40秒,由于FS01-3工位的取消,每班次精简了1名操作工。 2.以同样的方法,将操作时间超过TT90秒的主线FC06工位进行分析,将此工位内容进行分解,对作业进行了重新安排,将前后滑脚护板的锁紧工作分给了后一工序FC07,将FC06的操作时间减少了16秒,使生产线得到了更好的平衡。 3.因后面主线有整理工位,将FS02-6后靠背整理工位取消,通过工位的取消每班次节减了1名操作工。 4.对工位FS02-4背面上部及两侧挂钩安装的工作进行分解,背面上部挂钩安装挪到了FS02-3工位,悲悯两侧挂钩安装挪至工位FS02-5,取消了FS02-4工位,通过工位的取消,不仅减少了2名操作工(每班次1名),也是其前后两个工位FS02-3和FS02-5的工作更加饱满。 5.将FC10工位的安装头枕销工作挪到FQ01和FQ02这两个座椅检测工位,取消FC10工位,每班次减少了1名操作工,同时提高了后两个工位FQ01和FQ02的负荷率。 6.将FQ03的工作进行分解,将放置头枕的工作挪至前两个左右驾整理工位,将FQ03的SBR检测和FQ04的buckle、SAB等座椅安全件的检测合并,由此每班次减少了1名操作工。 通过以上工序流程的改善,X公司的#2座椅装配线得到了很好的改善效果,线平衡率提高了约25%,节省了10名操作员工。 (二)提高自动化率 随着科技的进步以及人力资源成本的不断提高,自动化成为了现代制造业的一大趋势。企业应该结合自身情况规划公司的自动化方向,从当前比较容易实现的地方开始实行,优化相应的生产流程,逐步地推进,满足精益生产的要求。公司精益团队设计并实施了部分自动化改进项目,比如前座椅螺钉紧固机器人、SubLine半成品传动带、搬运用机械手与机器人、自动喷码机、脱模剂喷涂机器人等。详情如表2所示: 表2 #2装配线自动化设备清单 ![]() 1.机械臂 改善前的前坐垫需要操作工拿起放到线旁的料架上以及工作台传送带上,坐垫半成品重量较重,人员劳动强度大。改善后由机械臂把半成品直接搬运至传送带上,缓解了员工的劳动强度。 2.传送带 副线生产的坐垫与靠背半成品改善前是放在线边的料架上,由物流上料人员搬运到主线相关工位。通过在副线和主线之间的上部空间连接两个半成品传送带传送坐垫及靠背半成品,不仅节省了副线线边半成品料架车及物料空间,还节省了主线线边的料架及存储空间,重要的是精简了4名物流上料人员,大大降低了人工成本。 3.靠背抓取机器人 副线增加了一台机器人,将组装的半成品靠背旋转并放到传送带上,主线首工位增加一个机器人,将半成品坐垫从传送带拿下,这不仅节省了两名操作员工,减少了线边的料驾车以及存储空间,也解决了此工位因劳动强度大造成的轮岗困难的问题。 4.自动螺钉拧紧机器人 半成品坐垫和靠背的固定由原来的人工操作,变更为机器人操作,不仅节省了人工成本,也提升了质量,减少了因为人工操作导致的错漏装问题。 通过上述几种对#2座椅装配线自动化设备的增加投入,不仅降低了了#2座椅装配线的人工成本,提高了生产效率,也使产品质量更加稳定。 5.发泡自动喷码机 在增加发泡自动喷码机之前,下线的发泡由质量部员工在发泡上人工加盖时间戳,两小时更换一次时间,时间不够准确。增加自动喷码机之后,产品下线时自动喷码,不仅节省了两名质量部员工,喷码时间精准,有利于发泡的先进先出。 6.喷脱模剂机器人 人工喷涂脱模剂的方式会造成大量的脱模剂因模具反弹而挥发,产生了不必要的脱模剂损失。此外,传统人工喷涂方式不仅工作强度大,也对操作者的健康不利。与人工喷涂不同的是,机器人静电喷涂方式利用电场使脱模剂粒子雾化带电,通过静电将脱模剂吸附到模具上,从而提高了脱模剂使用率。而且自动喷涂方式能为公司实现两名员工的节减,也降低了有害物质对员工健康的影响,还因机器人能够精确控制脱模剂使用量,从而节约了脱模剂使用成本。除此之外,机器人喷喷涂路径比较稳定,不会发生错喷漏喷等现象,也改善了泡沫质量。 7.自动清模机器人 机器人清模时可以同时做到大面积且力度强的清模,不会有残留物造成发泡的硬节等质量问题,能够有效确保清模质量。因可以两个方向进行上方模具与下方模具的清洁,不仅能提升发泡线效率,还能节省2名清模员工。 (三)快速换模 X公司有两个停线的主要原因,设备出现故障而导致的被动停线以及更换模具时的主动停线,对企业而言这是一种巨大浪费,因此需要企业利用快速换模(SMED)缩短停线时间。从现场考察的情况来看,X公司在换模过程中存在明显的浪费,可以通过缩短换模时间,取得明显改善效果。 以下通过对X公司发泡车间的换模流程为例,对发泡线的换模问题进行具体的分析。本文采用秒表对换模流程中的作业时间进行测定,并做好记录,测定次数为5次,求平均值为标准时间。 1.对换模流程中的内外部时间进行区分,以下表3为改善前换模步骤: 表3 优化前换模步骤表(部分) ![]() 2.在区分内部及外部换模时间后,需要考虑哪些内部换模时间可能被转换成外部换模时间。可以运营5W1H分析法进行提问,了解内部作业里每一步骤的目的和作用。通过现场考察和分析,发现部分换模工作可以在换模工作开始前提前准备到位,无需占用内部换模时间。例如:工序9确认安全劳保穿戴情况. 3.缩短内部切换时间 在区分内部和外部换模时间之后,需要考虑是否还有缩短内部换模时间的可能性,尽可能减少由于内部换模工作而造成的停线时间。本文运用ECRS和5W1H等工作流程改善分析方法,缩短了内部换模时间。具体改善步骤如下: (1)并行作业 通过对换模过程的探讨及分析,发现换模作业人员不足且岗位不固定是影响操作效率的主要原因。将原换模人员从4名增加到8名,并将人员站位及分工固定。在换模铃声响起后,4名卸模架车的人员到达换模具岗位,进行开门、挂锁、卸模架车等操作,并将模架车推至环线门口,同时另外4名换模人员去换模区将新模架车推到环线门口并接走卸下的不生产的模架车,安装人员将新模具推进环线进行安装时,另外四人将接走的模架车退至换模站。 (2)简化作业 进一步分析发现,安全上锁环节存在部分浪费。具体原因为上锁和解锁时由于只有一个锁孔,不便操作,且填写上锁及解锁记录耗时长,经过改进,将个人锁具锁在一个大的四孔专用锁具上,操作方便。另外将上锁及解锁记录格式由书写方式改为选择题方式,大大缩减了安全上锁解锁环节的时间。节省了52秒的内部时间。 4.缩短外部时间 改善前寻找需要切换的新模具时费时较长,因为模具只有编号,而模具存储架上有很多模具,很难快速准确查找到相应模具。通过改进,为模具赋予与模具编号一样的二维码,并在将模具存放到存储架上时与存储架相应存储位上的二维码进行绑定,需要寻找模具准确存储位置时,只需在电脑输入模具编码,即可查找到模具准确位置,大大提高了寻找新模具的时间。此外,将模温机从30kw变更为60kw,模具预热时间从20分钟降到了10分钟。 五、精益生产实施的效果评价 (一)生产线平衡效果评价 在优化#2座椅装配线线平衡的过程中,通过对工位进行取消、合并、重排、简化的ERCS方法,不仅消除了#2座椅装配线的瓶颈工位,而且使生产流程更加合理,提高了整条线的线平衡率。此外,通过此次生产线平衡的改善,该生产线操作员工也由原来的64人变更为54人(双班制,每班次5人),大幅降低了人工成本。以下表10为优化后的各工位操作时间: 优化后的生产线平衡情况如图2和表4所示,#2座椅装配线的线平衡率从改善前的62.43%提高到87.59%,人员从64人减少为54人。 ![]() 图2 优化后的线平衡图 表4 生产线平衡优化前后对比 ![]() (二)自动化改进效果评价 #2座椅组装线通过提高自动化率组装车间减少生产直接人员4人,物流上料人员4人,共节省了8人,年节约人工成本约年人民币768,000元。此外节省了周转用料驾车12个以及料驾车存储面积36m2,并且通过自动化率的提高,确保了产品质量。 发泡线通过自动化的改进不仅保证了产品质量的稳定,还减少了6名人工,节省了年人工成本576,000元,同时原材料也实现了年节省180,000元。 4.3快速换模效果评价 首先,X公司的发泡生产线换模工作通过结合发泡线换模工作的实际情况和快速换模理论,把部分换模工作的内部时间转化成换模外部时间,并采用5W1H和ECRS分析法,通过并行作业和简化工作的方法压缩内部换模时间。最后,通过模具电算化与设备功能的改进缩短了换模的外部时间。改善前的外部时间为1,765秒,换模内部时间为435秒。通过快速换模对此进行优化后,外部时间缩短为790秒,内部时间也降低到205秒。每天由于换模工作造成的停机时间也由原来的40多分钟缩短到20分钟左右。换模内部时间对比如图14所示: ![]() 图3 优化前后内部时间对比图 通过本次快速换模,使换模过程更具合理性。制定标准化的作业指导书(WorkIn-struction,WI),使操作者可根据标准化的文件进行换模作业,规范了换模工作。操作者通过参与到本次快速换模活动中,加强了他们对工作的了解,强化了员工的精益生产意识,有助于将来在公司推行更多的精益生产活动。 六、结论 本文以X公司为具体的研究对象,根据企业自身的特征,将精益生产理论灵活地运用到实际工作中,具体改善成果如下: (一)通过对#2装配线的线平衡分析及优化,运用ECRS及5W1H分析方法,使工位分配更加均衡化,不仅消除了瓶颈工位,还节省了人工成本,提高了装配线的生产效率。 (二)通过提高自动化率,保证了产品质量的稳定,组装线及发泡线的生产效率得到了有效的提升。此外,共计节省了年人工成本1,344,000元,同时原材料也实现了年节省180,000元。 (三)通过采用快速换模以及推行TPM,减少了发泡车间设备的停机时间,产品合格率及生产效率也得到了很大改善,发泡车间的OEE从78.89%提高到了84.96%。 参考文献: [1]刘斌强,张永钢,狄凯歌. SMED初探[J].中国印刷,2006(01): 80-81. [2]Gurumurthy A., Kodali R. Design of lean manufacturing systems using value stream mapping with simulation: A case study[J]. Journal of Manufacturing Technology Man- agement, 2011, 22(4): 444-473. [3]Kathleen E M A., Roger G S B., Kristy O C B. The impact of total productive mainte- nance practices on manufacturing performance[J]. Journal of Operations Management, 2001, 19(1): 39-58. [4]McCarthy D., Rich N. Lean TPM: A blueprint for change[J]. Maintenance & Engineering, 2015,15(2): 12-14 [5]陈艳君.基于精益造船的船舶生产设计管理流程[J].船舶物资与市场,2021(02):73-74. [6]何帆,都亚军,肖恭林.铸造企业推行精益生产方式的几点思考[J].铸造工程,2020,44(06):1-4. [7]肖雪峰,果伟,李硕,王珊珊.基于“七零”目标的现场精细化6S管理研究[J].企业改革与管理,2020(19):17-18. [8]李家毅.以“5+IE”模块推进精益生产的实践[J].数字通信世界,2020(10):275-276. |

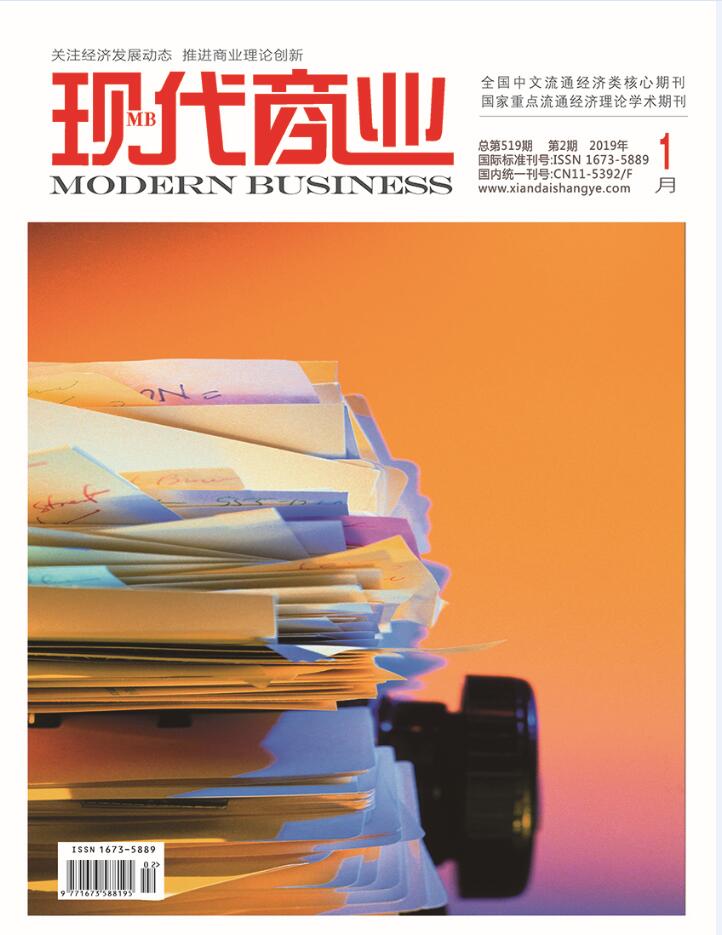
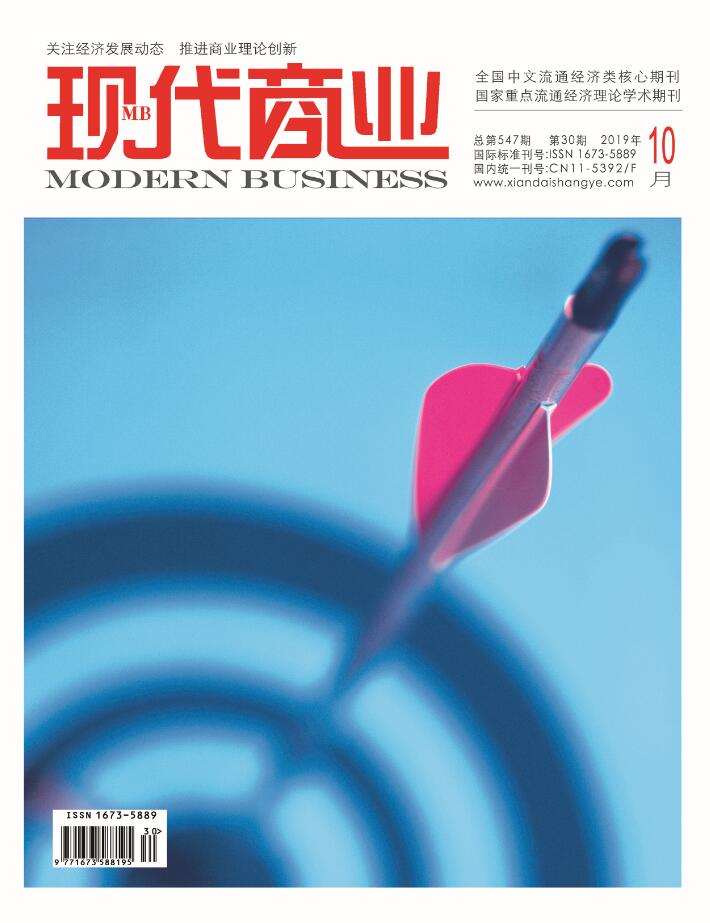