工业4.0背景下我国企业的智能制造之路
2016-09-24 22:34 来源:www.xdsyzzs.com 发布:现代商业 阅读:次
袁洪飞 上海杉达学院
基金项目:2015年上海高校示范性全英语教学课程建设《宏观经济学》
摘要:在分析智能制造及其生产特征和主要发达国家现阶段智能制造发展概况的基础上,结合企业案例,阐述了我国企业智能制造的主要制约因素,提出了我国企业实现产业升级和智能制造的路径。
关键词:工业4.0;智能制造;智慧工厂
随着新一轮科技革命和产业变革在全球的兴起,工业技术体系、发展模式和竞争格局正迎来重大变革。发达国家纷纷出台以先进制造业为核心的“再工业化”国家战略。如德国提出“工业4.0计划”旨在通过智能制造提振制造业竞争力,美国大力推动以“工业互联网”和“新一代机器人”为特征的智能制造战略布局,欧盟提出“2020增长战略”重点发展以智能制造技术为核心的先进制造业,日本、韩国等制造强国也各自提出发展智能制造的战略措施。可见,智能制造已经成为发达国家制造业发展的重要方向,成为各国发展先进制造业的制高点。我国在2015年推出的“中国制造2025”战略中也强调了智能制造的重要性。发展智能制造不仅是我国企业转型升级的突破口,也是重塑制造企业竞争优势的新引擎,是制造业的未来方向。
一、智能制造及其生产特征
智能制造是以新一代信息技术为基础,配合新能源、新材料、新工艺,贯穿设计、生产、管理、服务等企业内制造活动的各个环节甚至整个产业链,具有信息深度自感知、智慧优化自决策、精准控制自执行等功能的先进制造过程、模式与系统的总称。
(一)构建智能生产工厂
智能制造本质是通过端到端数据整合消除信息不对称,实现企业运营、价值链乃至产品全生命周期的数据连接和传递,打破企业内部各环节和企业间的连接壁垒,实现机器的协同、制造流程的协同以及价值链的协同。也就是说,工业企业旨在通过鼓励传统优势技术研发和新一代信息技术创新,打造一个将资源、信息、物品和人互联的信息物理系统(CPS),实现“智能生产”和“智能工厂”。新型的智能工厂基于信息物理系统并借助社交网络,可实现自然的人机互动,这将重塑传统制造工厂模式下人与生产设备之间操控与被动反应的机械关系。为达到此目的,需要在制造装备、原材料、零部件及生产设施上广泛植入智能终端,借助物联网不仅可实现终端之间的实时互动,自动信息交换,自动触发行动,而且可实施独立控制,对生产进行个性化管理和远程控制。
(二)整合智能工业系统
在构建工业生产的各种要素中,除了传统的土地、劳动、资本、企业家等要素之外,数据将成为一种重要的甚至是影响全局的生产要素。依托于信息物理系统,智能工厂生产出可实时生成数据的“智能产品”,形成大数据系统。大数据经过实时分析与归总后,形成“智能数据”,经过可视化和互动式加工,向智能工厂反馈产品和工艺流程的实时优化方案,从而形成“智能工厂—智能产品—智能数据”闭环,驱动生产系统走向智能化。而这一切的实现依赖于云技术等互联网基础设施的建设和高端信息技术的应用。智能工厂和智能产品构成嵌入式制造系统,该系统的特点是:企业间的业务流程构成横向价值链,企业内部的运营流程构成纵向价值网络,终端到终端技术实现横向和纵向的整合。在智能工厂的基础上,通过物联网和服务联网,将智能交通、智能物流、智能建筑、智能产品和智能电网等相互连接,以新型工业化和信息化实现经济社会系统的全面智能化。
二、主要发达国家智能制造发展概况
20世纪80年代末,信息技术尚未对人类生产生活产生巨大影响之时,智能制造的概念就已被欧美日等发达国家提出。进入新世纪之后,实现智能制造的技术和成本条件成熟,并且,随着资源环境压力加大、劳动成本上升等制造业制约因素的增强,智能制造市场近年来在全球出现了爆发增长并呈现新的特征。国际金融危机后,为刺激本国经济增长,重塑实体经济的竞争力,许多发达国家都实施了一系列国家战略,例如德国的“工业4.0”计划、美国的“先进制造业伙伴计划”、日本的“再兴战略”、韩国的“新增长动力战略”、法国的“新工业法国”等。美国和德国的智能制造基本情况如下:
德国工业4.0构建智能生产系统。2010年,德国发布《高技术战略2020》,着眼于未来科技和全球竞争,并将工业4.0战略作为十大未来项目之一。2013年,德国联邦教研部与联邦经济技术部联手正式发布《保障德国制造业的未来:关于实施“工业4.0”战略的建议》,得到了德国工程院、弗劳恩霍夫协会、西门子公司等德国学术界和产业界的响应和推动,从而上升为国家级战略。
美国为重振本国制造业,密集出台了多项政策文件,重新规划未来的制造业发展,意图抢占新一轮技术革命领导权,通过发展智能制造重塑国家竞争优势。2011年奥巴马政府提出“先进制造伙伴计划”,并由全球顶尖的技术和服务业务巨擘GE提出了“工业互联网”的概念,以智能制造弥补劳动力成本劣势。工业互联网以互联网络为基础,通过软件控制应用和软件定义机器的紧密联动,促进机器之间、机器与控制平台之间、企业上下游之间的实时连接和智能交互,最终形成以信息数据链为驱动,以模型和高级分析为核心,以开放和智能为特征的工业系统。
三、国外智能制造企业案例分析
在德国几乎所有大型自动化企业和上千家中小企业都加入到工业4.0体系。其中,西门子安贝格工厂就初步展示了智能工厂的雏形,其独特之处在于拥有数字化的制造车间和一套高度数字化的生产流程。其研发和制造都基于同一个数据平台,意味着研发和生产几乎可以同步进行,这颠覆了传统制造的节奏。工厂的生产设备和计算机可以自主处理75%的生产流程,剩余25%的工作则由人工完成,人的作用不再是直接从事一线生产,而是主要负责进行生产规划和监督机器是否高效运转。在系统中,任意数据发生更新,质量、采购、物流等不同部门都能第一时间获得最新信息,避免了传统研发制造企业的研发和生产环节或不同部门之间由于数据平台不同造成的信息“脱节”。据了解,安贝格工厂车间有10条生产线,1000余名员工年产上千种工控产品,平均每秒就能生产出1件产品。如此高效率的生产却进行得有条不紊。Gartner的调查称,工厂每100万件产品中的残次品数量只有15件,生产线的可靠性达到99%,可追溯性高达100%。
西门子工业自动化产品成都生产及研发基地(SEWC)是西门子另一家先进的自动化产品生产研发基地,被称为安贝格姊妹工厂,其内部实现了从管理、研发、生产到物流配送全过程的数字化,并与德国生产基地和美国的研发中心实现了数据互联。通过数字化模拟和传真,SEWC节省了制作样机的时间,源自设计人员的修改可实时传输到生产线上。
无独有偶,实施智能化改造的工业巨擘GE公司,将其设在美国的氯化镍电池工厂建成了首家集成工业互联网应用的“样板工程”。这座电池工厂的日常工作无疑是一场成功的动态过程控制实践。在工厂生产厂区内,GE共部署了1万多个传感器,它们分布在生产线的不同环节,分别用来检测电池制造生产线的温度、制造电池所耗费的能源、电池生产车间的气压,甚至查询生产线的产能。这些实时采集的数据通过内部高速以太网传输到GE的云数据平台进行集中处理。跟踪这些数据信息,GE可以通过动态过程控制诊断电池生产问题,降低故障几率,同时弹性调节流水线传输速度。有资料显示,这种动态的过程控制使GE的生产灵活性和效率提升了15%以上。在生产线之外,管理人员通过工厂Wi-Fi网络获取这些传感器发来的数据,及时跟踪设备信息,监督生产过程。GE还计划在电池中加装芯片,跟踪电池出厂后使用状况,提前制定生产优化或维修计划。
综观以上西门子、GE等国外智能制造先行者的实践可以发现,智能化不仅有效提高了能源使用效率,减少了资源的浪费,而且大幅提高了工业系统设备的维护修复效率,延长了设备寿命,还优化了工业领域整体生产运营效率。
四、我国企业推动智能制造的主要制约因素
我国传统的制造企业认识到智能化的趋势,在生产流程和新业态、新模式方面进行了有益的探索。目前我国不少企业仍处于自动化改造阶段,如何从自动化加速向智能化迈进,是推进智能制造过程中最为核心的问题。更何况很多企业自动化改造尚未完成,如国内离散行业数控设备达到60%已是较高水平,大部分做智能制造的企业先要解决的是机器换人问题。而自动化还只是智能制造的第一步,要达到智能制造的水平,在实现自动化之后,还有精益生产、数据建模、端到端数据链打通和基于数据分析的智能化等环节。所以我国企业要达到智能制造的“境界”可谓任重道远,制约因素也很多。
我国工业化起步晚,技术积累相对落后,先进技术的产业化能力与发达国家存在显著差距,致使国产智能制造产品和系统的发展同时面临技术和市场的瓶颈。
(一)关键零部件依赖进口造成价格倒挂
以智能制造最核心的装备——工业机器人为例,目前我国精密减速机、控制器、伺服系统以及高性能驱动器等机器人核心零部件占整体生产成本70%以上,但大部分依赖进口。其中,精密减速器75%的份额被日本垄断,高价购进后已占生产成本的45%,而在日本仅为25%。我国核心零部件的采购成本就已高于国外同款机器人的整体售价,在高端机器人市场上根本无法与国外品牌竞争。绝大多数国内机械零部件企业都只能生产低端产品,无法满足高端智能装备产业发展的要求,而这些产业的升级远比组装装配环节的制造业困难得多,所需时间也更漫长。短期内我国智能制造装备企业的发展仍需依赖国外采购,但必须降低进口部件采购成本,实现采购渠道的稳定和多元化。
(二)软件系统发展滞后
长期以来,我国重硬件制造、轻软件开发的思维十分普遍,智能制造装备生产企业的软件技术积累严重不足。智能制造基础软件系统的开发仍十分匮乏,国产数控机床、机器人等高端产品还大量使用国外软件系统,在跨国公司布局智能制造装备模块化生产和操作系统研发时,我国的智能制造装备产业仍面临基础操作系统缺失的情况。
(三)跨国公司垄断势力挤压国内企业发展空间
全球智能制造产业的垄断势力已基本形成,我国虽已成为全球最大的智能制造装备的需求市场,但70%以上的市场被几家国际巨头占据,90%的高端市场依赖进口,国内还没有一家具有全球影响力的智能制造企业。近年来,随着我国工业机器人等智能装备市场的增长提速,跨国公司加快了在国内的战略布局,以合资或独资形式在我国经济发达地区建设工厂,这对带动我国智能制造产业的发展和技术进步起到一定的作用,但同时也进一步挤压国内自主品牌企业的市场空间。
五、我国企业智能制造的发展之路
我国企业在智能化方面与发达国家的领先企业相比差距巨大,但新科技革命也为我国企业发展智能制造及产业升级带来重大机遇。我们应把握“机会窗口期”,积极总结和借鉴国外先进经验,以智能制造为突破口推动我国企业技术升级,实现制造企业竞争优势由传统要素优势向技术优势的转型。
(一)将基础系统软件的开发和标准的制定纳入到顶层设计中
未来智能制造的发展将围绕软件系统展开,我国之所以要从国外进口高端装备和成套生产线,一个重要原因就是缺乏自主工艺数据库和专家系统,这是我国发展智能制造产业的短板。因此,必须重视基础软件系统和标准的制定,形成自主的智能制造产业制高点,避免在硬件制造中再次受制于国外操作系统。
(二)加强关键核心技术攻关,打造国产机器人自主品牌
我国的机器人产业起步较晚,由于发展阶段、条件和目标不同,机器人产业很难也不能再走传统“市场换技术”的老路。应大力推动核心关键技术的攻关项目,加强对技术研发成果的知识产权保护。同时,培育具有国际影响力的机器人骨干企业,发展一批创新力强的中小型企业,提升国产自主品牌的国际竞争力。
(三)大力培养技能工人,注重利用全球人才资源
从美国的《重振美国制造业框架》到《先进制造业伙伴计划》,再到《先进制造业国家战略计划》,都把提高劳动者素质作为重要的政策内容,通过培训工人提高其劳动技能,以适应先进技术发展的需要。我国也要大力发展满足智能制造要求的职业技能教育和培训,以不断适应制造业变革的技能要求,同时还要吸引全球制造业人才,尤其是高层次人才,利用全球人才资源发展中国智能制造。
(四)完善落实相关配套政策,大力鼓励技术创新
美日欧等发达国家的先进制造业都获得了政府的大力扶持,财政资金也大量向研发创新倾斜。例如,日本在2006~2010年间为了攻克关键的服务机器人技术每年投入1000万美元,美国联邦政府当前对每个制造业创新研究资助7000万至1.2亿美元。为扶持智能制造产业的发展,我国也应从多个方面完善落实相关配套政策:加大财政和税收方面的扶持力度,建立智能机器人研发风险准备金,激发制造业企业创新活力;加大对国产智能制造装备的政府采购,给予这个幼稚产业一定的保护期;在部分地区、部分行业开展智能制造试点示范,探索新模式、新方法,并逐步推广普及。
参考文献:
[1]李培根.中国制造2025:“智”造蜕变[J].企业研究.2015(08)
[2]王天然.机器人助力中国智能制造[J].科技导报.2015(23)
[3]朱森第.我国智能制造与智能制造装备的发展[J].冶金管理.2015(09)
[4]周济.智能制造——“中国制造2025”的主攻方向[J].中国机械工程.2015(17)
|

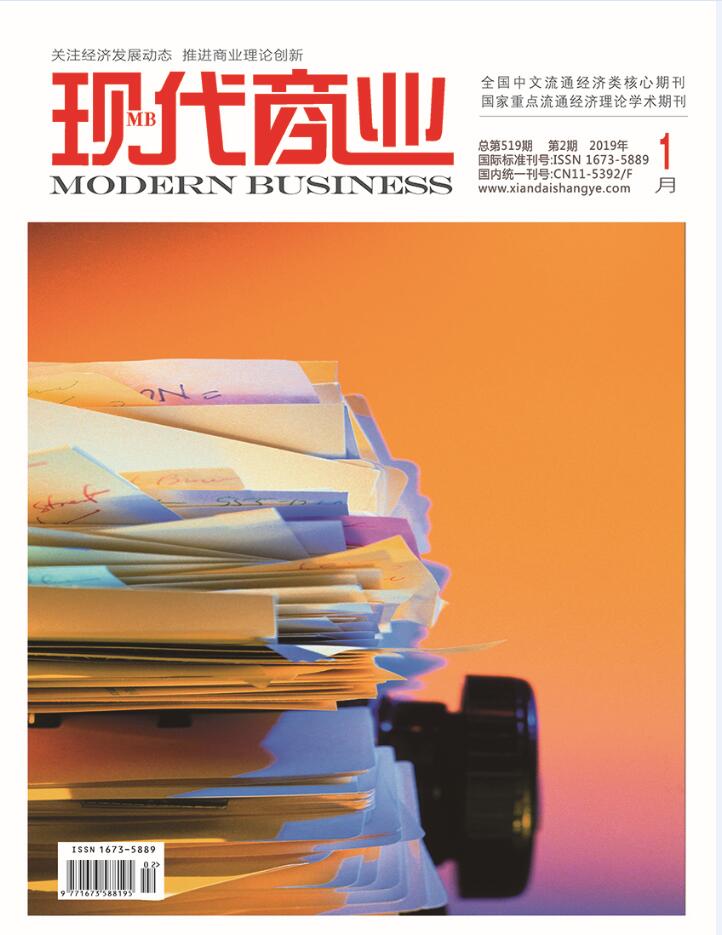
热点阅读
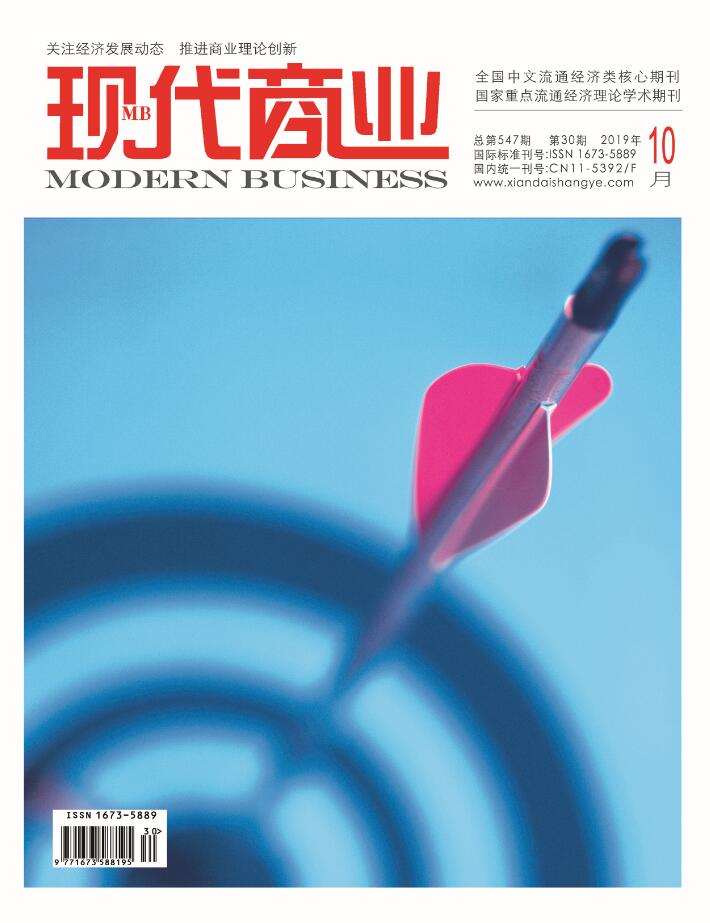
相关内容
发表评论